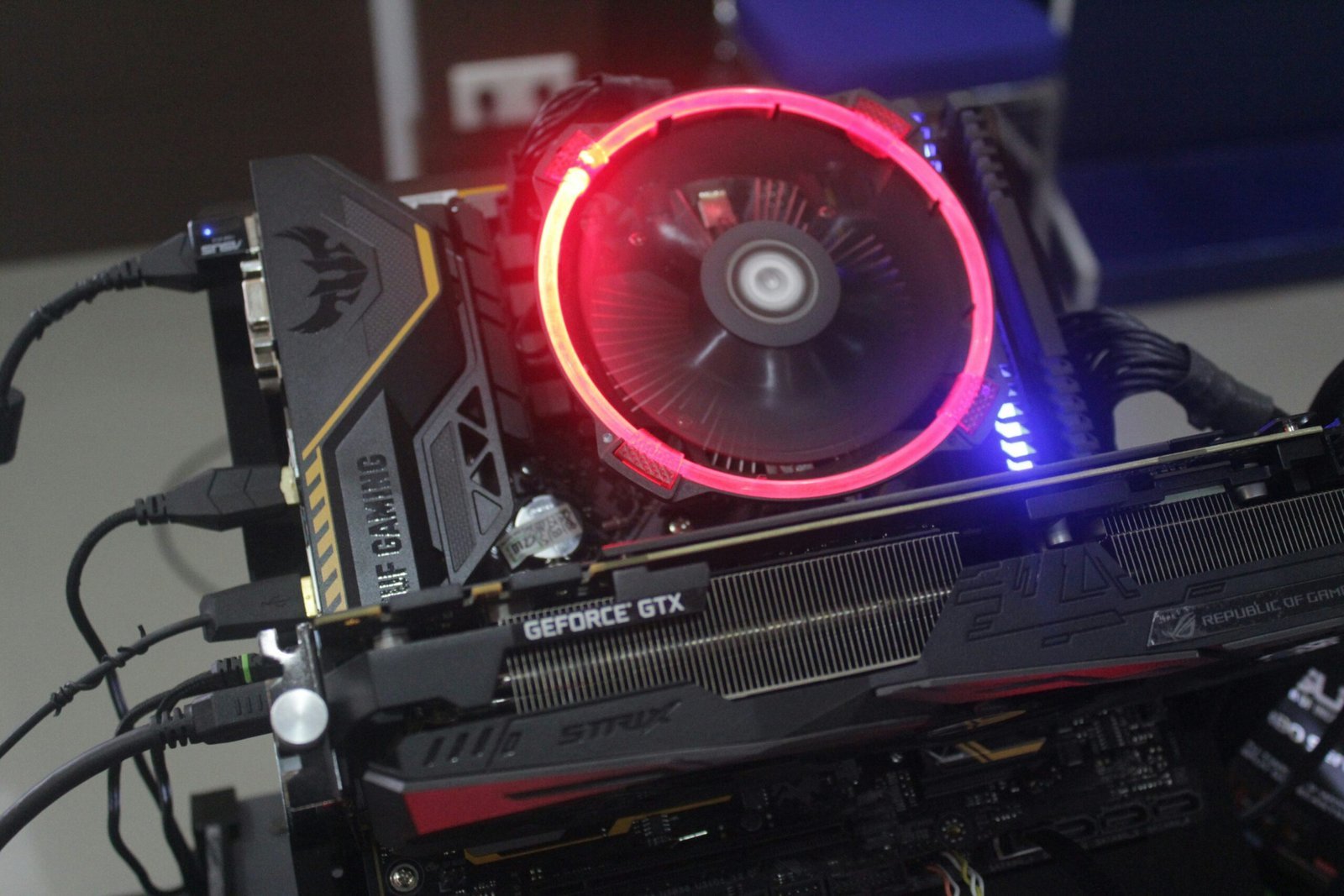
Understanding Equipment Failures
Equipment failures represent a significant challenge in various industries, leading to costly downtime and operational inefficiencies. A thorough understanding of these failures is essential for effective asset management. Common causes can be categorized into mechanical and electronic issues, each contributing to reliability challenges. Mechanical failures often arise due to wear and tear, improper lubrication, or fatigue in materials. Over time, components can degrade, resulting in unexpected breakdowns that hinder a system’s optimal performance.
On the other hand, electronic failures typically involve issues such as circuit board malfunctions, sensor inaccuracies, or software glitches. These electronic problems can disrupt the operation of sophisticated machinery, highlighting the importance of integrating robust engineering solutions during the design phase. Understanding the root causes of both mechanical and electronic failures is critical for effective problem-solving strategies.
Moreover, environmental factors play a crucial role in equipment longevity. Extreme temperatures, humidity levels, and exposure to corrosive substances can significantly impair equipment performance. Therefore, organizations must consider the environmental context when developing their maintenance practices and longevity assessments. Additionally, usage conditions, including overloads and incorrect operational practices, can exacerbate mechanical or electronic issues, demonstrating the importance of training operators to adhere to best practices.
By analyzing these contributing factors to equipment failures, companies can formulate proactive strategies aimed at optimizing their asset management frameworks. Each element of failure not only serves as a warning sign but also presents an opportunity to enhance reliability through targeted engineering improvements, leading to a more resilient operational environment. This foundational understanding paves the way for the development of preventive measures and mitigation strategies essential for maintaining equipment functionality.
The Impact of Equipment Failures on Operations
Equipment failures can have profound effects on business operations, manifesting in both direct and indirect ways. The immediate consequence of an equipment malfunction is typically operational downtime, which can lead to significant financial losses. For instance, a manufacturing company experiencing a machine breakdown may halt production lines, incurring thousands of dollars in lost revenue for every hour of delay. These financial implications are compounded by the potential costs associated with emergency repairs and the need to expedite replacement parts, all of which strain the budget.
Beyond the immediate financial burden, equipment failures can also disrupt workflow and adversely affect productivity. In industries relying heavily on machinery, such as construction and manufacturing, the unavailability of equipment can lead to scheduling delays. This is not just a question of lost time but can also result in missed opportunities and an inability to meet client demands. As deadlines are pushed back, businesses may find themselves in a position where they risk losing contracts and damaging long-term relationships with clients.
Furthermore, the ripple effects of equipment failures extend to employee morale. Continuous breakdowns may create a work environment characterized by frustration and uncertainty. Workers dependent on reliable equipment for their tasks may experience stress and dissatisfaction when faced with frequent interruptions. This disengagement can lead to decreased productivity and increased turnover rates, further exacerbating operational challenges. Thus, ensuring equipment reliability is not merely a technical concern but a pivotal aspect of effective management that influences the overall performance and culture of the organization.
Real-world examples underscore the critical need for proactive strategies in asset management, emphasizing the importance of reliable engineering and problem-solving approaches to optimize operational workflows. Companies that invest in predictive maintenance and robust equipment management systems often witness a measurable improvement in their operational efficiency, fostering a more resilient workforce.
Preventive Maintenance: A Key to Reliability
Preventive maintenance plays a crucial role in enhancing the reliability of equipment and assets across various engineering sectors. By implementing a structured maintenance schedule, organizations can significantly reduce the likelihood of unexpected failures that disrupt operations. The essence of preventive maintenance lies in its proactive approach, which aims to identify potential problems before they escalate into costly breakdowns.
One of the best practices in developing a robust maintenance schedule involves thorough training for maintenance staff. Educating employees on equipment handling and common failure modes can empower them to spot issues early. Additionally, training should include insights into asset management, ensuring that technicians are not just reactive problem solvers but also strategists in maintaining reliability. A well-informed staff can contribute to a culture of accountability and continuous improvement.
Regular inspections form another cornerstone of preventive maintenance. Scheduled checks allow for the close monitoring of equipment conditions and the timely detection of wear and tear. During these inspections, it’s advisable to utilize checklists that cover all vital components. This systematic approach enables engineers to adhere to industry standards while optimizing the maintenance process. Transitioning from routine inspections to more advanced methodologies such as predictive maintenance can also enhance reliability. Utilizing technology, such as sensors and data analytics, organizations can forecast equipment failures before they occur, thus saving resources and extending the lifespan of assets.
In conclusion, embracing a comprehensive preventive maintenance strategy focused on training, regular inspections, and technological integration is vital in optimizing equipment reliability. By prioritizing these best practices, organizations not only enhance the dependability of their assets but also significantly mitigate operational risks associated with equipment failures.
Identifying Early Warning Signs of Equipment Failure
Recognizing early warning signs of equipment failure is crucial for effective management of assets in any engineering context. Early detection allows for timely intervention, ultimately enhancing reliability and reducing downtime. A proactive approach begins by closely monitoring performance metrics that serve as indicators of an asset’s health. These metrics may include temperature readings, pressure levels, and operational speeds, which should be compared against established benchmarks to determine abnormal trends.
Incorporating advanced diagnostic tools can significantly aid in problem-solving efforts related to equipment failures. Technologies such as vibration analysis and thermal imaging can provide insight into the mechanical condition of machinery. Vibration analysis, for instance, helps in identifying irregular patterns that could indicate misalignments or wear. Similarly, thermal imaging can reveal overheating components that may lead to catastrophic failures if not addressed promptly. Utilizing these tools not only helps in diagnosing potential issues but also optimizes the maintenance schedule, ensuring that resources are efficiently deployed.
Furthermore, understanding common sound or vibration anomalies can provide valuable information regarding asset performance. Equipment should operate within a specific sound range; any deviations, such as unusual grinding, squeaking, or rattling noises could signal impending failure. Likewise, vibrations that exceed normal thresholds often indicate an underlying problem. By training personnel to recognize these signs, facilities can enhance their reliability and efficiency in managing engineering assets.
In summary, the integration of performance monitoring, diagnostic tools, and auditory/vibrational analysis equips organizations to identify the early warning signs of equipment failure. This proactive stance not only minimizes risks but also sets the foundation for effective asset management and long-term reliability.
Effective Troubleshooting Techniques
Troubleshooting equipment failures is a critical skill in the realm of engineering and asset management. A systematic approach is essential to diagnose and resolve issues efficiently, ensuring reliability and optimal performance. The first step is to clearly define the problem; gathering detailed information about the failure, including symptoms, timeframe, and conditions under which the failure occurred, is vital. This data sets the foundation for effective problem-solving.
Once the issue is defined, employing a step-by-step investigative process can greatly enhance the troubleshooting experience. Start by utilizing checklists tailored to the specific type of equipment in use. These checklists should cover common failure points and maintenance practices, enabling technicians to swiftly narrow down potential causes. By methodically moving through the checklist, the investigator can isolate the problem area, which saves time and resources.
Leveraging technical documentation is another critical component of effective troubleshooting. Equipment manuals often contain valuable information regarding the design and operation of the machinery, offering insights into known issues and previous solutions. Access to online support resources, including forums and manufacturer support channels, can also prove beneficial. Engaging with others who have tackled similar problems can yield practical solutions and alternative strategies that one might not have considered.
Documentation of past equipment failures, their resolutions, and the troubleshooting processes followed can significantly optimize future operations. This creates a repository of knowledge that assists teams in avoiding repetitive issues while refining their troubleshooting techniques. By adopting a structured approach to diagnosing equipment failures, organizations can improve reliability while enhancing the overall efficiency of their asset management strategies.
Creating a Contingency Plan for Equipment Failures
In the field of engineering and asset management, the development of a comprehensive contingency plan is crucial for mitigating the impacts of equipment failures. A well-structured contingency plan not only enhances the reliability of operations but also provides a clear framework for problem-solving in the event of unexpected disruptions. To create an effective plan, organizations should follow several essential steps.
Firstly, it is vital to establish clear lines of communication among all stakeholders involved in the engineering and asset management processes. This ensures that everyone is informed when equipment failures occur, and decisions can be made swiftly. Assigning designated roles for communication will enable a more organized response to problems as they arise.
Next, identifying critical equipment within operations is a key component. This involves assessing which assets are essential for maintaining productivity and the overall workflow. By understanding which equipment is most vital, teams can prioritize their response strategies and allocate resources effectively. Additionally, it is beneficial to conduct regular assessments to determine the reliability of equipment and identify any vulnerabilities that may necessitate alternative solutions.
Outline alternative workflows that can be activated during equipment failures. This means developing detailed procedures for transitioning to backup systems or redirecting tasks to minimize downtime. Organizations might consider investing in redundant systems or cross-training employees, which allows them to adapt to various roles in the face of equipment issues.
Finally, testing and revising the contingency plan regularly is essential. Conducting drills or simulations can help ensure preparedness and optimize the plan over time. By continually refining the strategies in place, organizations can maintain operational reliability and effectively address any challenges posed by equipment failures.
Investing in Quality Equipment: Long-term Solutions
Investing in high-quality equipment is a foundational strategy in asset management that significantly enhances reliability and minimizes the risk of failures. The paramount importance of selecting superior equipment cannot be overstated, as the consequences of machinery breakdowns can lead to operational delays, increased maintenance costs, and ultimately, a negative impact on productivity. High-quality equipment is generally engineered to withstand the rigors of daily usage, providing consistent performance and reducing the frequency of repairs.
When considering new equipment, conducting a cost-benefit analysis is essential for informed decision-making. This analysis should encompass not only the initial purchase price but also long-term operational costs, including maintenance, energy consumption, and potential downtime associated with equipment failures. While cheaper alternatives may seem financially appealing at first glance, their lower reliability can lead to higher costs in the long run due to frequent repairs and reduced efficiency. Investing in durable equipment is often justified through lower total cost of ownership and the ability to optimize overall operational efficiency.
Furthermore, innovations in engineering have resulted in the development of advanced technologies that enhance equipment longevity. Many manufacturers now incorporate features that improve reliability, facilitating better performance under varied operational conditions. These advancements not only extend the lifespan of the assets but also improve their reliability, making them a sound investment for businesses committed to maximizing productivity.
Incorporating high-quality equipment into your operations is a proactive approach to problem-solving in the context of asset management. By prioritizing reliability and investing in superior machinery, organizations can mitigate the risks associated with equipment failures and create a more robust operational framework that supports long-term success.
Training and Empowering Staff to Handle Equipment Failures
Effective asset management is crucial in minimizing equipment failures and ensuring operational reliability. One of the key strategies to enhance the performance of any engineering scheme is to emphasize the importance of training and empowering staff members. Staff who are knowledgeable about their tools and machinery are more equipped to quickly identify and address potential problems, thereby reducing downtime and increasing reliability.
Creating a comprehensive training program should be the first step in empowering employees. This program should encompass an overview of equipment functions, identifying common failures, and understanding emergency procedures. Integrating simulation training can also be beneficial, allowing staff to engage in hands-on problem-solving experiments. Such realistic training scenarios prepare employees to respond effectively during actual equipment failures.
Ongoing education is another critical component of staff empowerment. Regular training sessions not only help refine existing skills but also introduce staff to the latest technological advancements and techniques in asset management. This could involve workshops, online modules, or guest lectures from industry experts. By fostering a culture of continuous learning, employees feel valued and motivated to take initiative when faced with equipment issues.
Furthermore, it is vital to create an environment where staff can voice their insights regarding equipment maintenance and reliability. Encouraging employees to contribute their observations empowers them to take ownership of their roles, transforming staff from passive participants to proactive problem solvers. This approach fosters teamwork and enhances operational efficiency.
In conclusion, training and empowering staff to handle equipment failures is not just an operational necessity but a strategic advantage. Investing in employee development not only enhances asset management but also cultivates a reliable workforce capable of addressing and solving engineering challenges. Through robust training programs and ongoing education, organizations can ensure they are prepared to handle any equipment issues that may arise, ultimately leading to more optimized operations.
Learning from Equipment Failures: Continuous Improvement
Continuous improvement is an essential principle in effectively managing equipment failures. This approach not only addresses immediate issues but also seeks to enhance the overall reliability of assets through systematic analysis and problem-solving. To maximize the effectiveness of management strategies, organizations should adopt a structured method to evaluate the causes of equipment failures. This begins with conducting thorough root cause analyses, which can uncover underlying factors that contribute to performance deficiencies.
Once a failure has been documented, it becomes crucial to synthesize the lessons learned from each incident. Engaging cross-functional teams in discussions can provide diverse perspectives on how similar problems may arise in the future, as well as insights into preventive measures. By incorporating feedback from various engineers, technicians, and operators, organizations can develop a more comprehensive understanding of equipment behavior and its demands under different conditions.
Another key aspect of fostering a culture of learning involves embracing a proactive mindset towards maintenance practices. This can entail regular training sessions and workshops focused on enhancing the engineering capabilities of staff, ensuring that everyone is equipped with the tools and techniques necessary to optimize asset reliability. Furthermore, utilizing data analytics to assess equipment performance trends will enable organizations to identify potential failures before they occur, reinforcing the importance of a preventative approach to asset management.
Building a framework for continuous improvement not only mitigates equipment failures but also empowers organizations to adapt and evolve in a constantly changing landscape. By prioritizing learning and knowledge sharing, companies can significantly improve their problem-solving abilities, leading to enhanced operational efficiency and reduced downtime. In conclusion, organizations that diligently apply the lessons learned from past equipment failures will foster a resilient environment, ultimately supporting sustained success and heightened asset reliability.